LASERs for manufacturing
What is LASER
Laser technology is extensively used in manufacturing processes across various industries due to its precision, versatility, and efficiency. Here are some common applications of lasers in manufacturing:
1. Cutting and Drilling: Lasers are widely used for cutting and drilling a variety of materials, including metals, plastics, ceramics, and composites. Laser cutting offers high precision, narrow kerf widths, and the ability to cut intricate shapes without physical contact. It is commonly used in industries such as automotive, aerospace, electronics, and sheet metal fabrication.
2. Welding and Joining: Laser welding is a fast and precise method for joining metal components. It offers deep penetration, minimal heat-affected zones, and high welding speeds. Laser welding is used in automotive manufacturing, electronics assembly, medical device production, and various other applications where precise and reliable welds are required.
3. Marking and Engraving: Laser marking and engraving provide permanent and high-quality markings on a wide range of materials, including metals, plastics, glass, and ceramics. It is used for product branding, serial numbers, barcodes, decorative engraving, and traceability in industries such as automotive, electronics, packaging, and jewelry.
4. Additive Manufacturing: Laser-based additive manufacturing, commonly known as laser 3D printing or selective laser melting, uses lasers to selectively fuse powdered materials layer by layer to create complex 3D objects. It is used in industries like aerospace, medical, and automotive for rapid prototyping, customized production, and lightweight part manufacturing.
5. Surface Treatment and Texturing: Lasers are employed for surface treatment processes such as laser cleaning, laser hardening, laser peening, and laser texturing. Laser surface treatment improves material properties, enhances surface finishes, and provides unique textures for aesthetic or functional purposes. These processes find applications in industries like automotive, aerospace, mold-making, and consumer goods.
6. Microfabrication and Micromachining: Lasers enable the precise micromachining of intricate features and structures on a small scale. This is valuable for manufacturing microelectronics, microfluidic devices, sensors, medical implants, and other micro-scale components used in various industries.
7. Inspection and Quality Control: Lasers are utilized for non-destructive testing, dimensional measurement, and quality control in manufacturing. Laser-based measurement systems, such as laser scanners and laser profilometers, enable fast and accurate dimensional inspection of parts, surface roughness measurement, and detection of defects or deviations.
These are just a few examples of the applications of lasers in manufacturing. The versatility and flexibility of laser technology make it a valuable tool in various processes, enabling precise, efficient, and innovative manufacturing solutions.
Benefits
Using lasers in manufacturing processes offers several benefits that make it a preferred choice in various industries. Here are some key benefits of using lasers in manufacturing:
1. Precision: Lasers provide exceptional precision and accuracy, allowing for the fabrication of intricate and complex parts with tight tolerances. The focused laser beam enables precise control, resulting in high-quality and consistent outcomes.
2. Versatility: Lasers can be utilized to process a wide range of materials, including metals, plastics, ceramics, composites, and more. They can perform cutting, welding, drilling, marking, engraving, and surface treatment operations, making them highly versatile for diverse manufacturing applications.
3. Non-Contact Process: Laser manufacturing is a non-contact process, meaning there is no physical force or tool-to-workpiece contact involved. This eliminates the risk of mechanical damage to delicate or sensitive parts and reduces wear on tools, resulting in improved longevity and reduced maintenance costs.
4. High Speed and Productivity: Laser processes can be highly efficient and enable high-speed manufacturing. The ability to rapidly move the laser beam across the workpiece, combined with the high power density of the laser, allows for fast and productive operations, reducing production cycle times.
5. Minimal Heat-Affected Zone (HAZ): Lasers generate a concentrated heat source that minimizes the heat transfer to the surrounding material. This results in a small heat-affected zone, reducing the risk of thermal distortion, stress, or damage to the workpiece. It is particularly advantageous for heat-sensitive materials.
6. Flexibility and Design Freedom: Laser processes offer design flexibility, allowing for the production of intricate and complex geometries that may be difficult or impossible to achieve with traditional manufacturing methods. This design freedom enables innovation and customization in product development.
7. Reduced Post-Processing: Laser manufacturing often produces high-quality surface finishes, reducing the need for extensive post-processing steps such as grinding, polishing, or deburring. This saves time, labor, and resources, leading to increased overall productivity.
8. Automation and Integration: Lasers can be easily integrated into automated manufacturing systems, enabling lights-out operation and continuous production. Laser systems can be programmed, controlled, and monitored digitally, facilitating seamless integration into Industry 4.0 and smart factory environments.
9. Environmental Friendliness: Laser manufacturing processes generate minimal waste and typically require fewer consumables compared to traditional methods. They can be more energy-efficient, resulting in lower energy consumption and reduced environmental impact.
10. Quality and Consistency: Laser processes provide consistent and repeatable results, ensuring high-quality manufacturing outcomes. The precise control over parameters such as power, speed, and focus allows for consistent part dimensions, surface finishes, and mechanical properties.
These benefits make lasers a valuable tool in modern manufacturing, enabling enhanced productivity, quality, and flexibility in various industries ranging from automotive and aerospace to electronics and medical devices.
Design specifications
When designing for manufacturing processes that involve lasers, it is important to consider specific design specifications to optimize the manufacturing outcomes. Here are some key design considerations for manufacturing with lasers:
1. Material Selection: Identify the appropriate material for your application that is compatible with laser processing. Consider factors such as the material's optical properties, thermal conductivity, and melting point. Common materials used in laser manufacturing include metals, plastics, ceramics, and composites.
2. Design for Laser Cutting or Welding: If your intention is laser cutting or welding, design the parts with appropriate features and geometry to optimize the process. Ensure that the design allows for efficient laser beam delivery and access to all necessary cutting or welding locations.
3. Tolerances: Define the required dimensional tolerances for your parts or components. Laser processes can achieve high precision, but it is important to specify the acceptable range to ensure the parts meet your functional and assembly requirements.
4. Feature Sizes and Resolutions: Consider the minimum feature size and resolution that can be achieved with the laser process. This is particularly important for applications such as laser engraving, microfabrication, or additive manufacturing where fine details or micro-scale structures are desired.
5. Surface Finish Requirements: Specify the desired surface finish for the laser-processed parts. Laser processes can result in varying surface roughness, so clearly define the acceptable range or specify additional post-processing steps if a specific surface finish is critical.
6. Laser Parameters: Provide guidelines or constraints for laser parameters such as power, pulse duration, wavelength, and spot size. These parameters can be tailored to optimize the process for specific materials, desired cutting or welding speeds, or other requirements.
7. Safety Considerations: Design with safety in mind. Consider any necessary safety features, such as enclosures, laser interlocks, or protective barriers, to ensure the safe operation of the laser system and protect personnel from laser hazards.
8. Assembly and Integration: Consider how the laser-processed parts will be integrated or assembled into the final product. Ensure that the laser processing does not introduce issues or limitations that could affect subsequent assembly steps or functionality.
9. Design for Quality Control: Incorporate features that facilitate inspection and quality control processes, such as clear marking areas, reference features, or registration marks. This helps ensure accurate and efficient inspection and verification of the laser-processed parts.
10. Manufacturing Constraints: Understand the specific constraints and capabilities of the laser manufacturing equipment and processes available to you. Collaborate with laser manufacturing experts to optimize the design for the specific laser system and its capabilities.
By considering these design specifications, you can enhance the manufacturability, quality, and efficiency of laser-based manufacturing processes, leading to successful outcomes and optimized production.
APPLICATIONS
Lasers have numerous applications in manufacturing processes across a wide range of industries. Some common applications of lasers in manufacturing include:
1. Laser Cutting: Lasers are widely used for precise cutting of various materials, including metals, plastics, ceramics, and composites. Laser cutting is employed in industries such as automotive, aerospace, electronics, and sheet metal fabrication to create intricate shapes and profiles.
2. Laser Welding: Laser welding is utilized for joining metal components with high precision and minimal heat input. It is commonly employed in industries like automotive, aerospace, electronics, and medical devices to achieve strong and reliable welds.
3. Laser Marking and Engraving: Lasers provide permanent marking and engraving on a variety of materials, including metals, plastics, glass, and ceramics. Laser marking is used for product branding, identification, serialization, and aesthetic customization in industries ranging from automotive and electronics to jewelry and packaging.
4. Laser Additive Manufacturing: Also known as 3D printing or selective laser melting, laser additive manufacturing enables the production of complex 3D objects by selectively fusing powdered materials layer by layer. It is used in industries such as aerospace, medical, and automotive for rapid prototyping, customized production, and lightweight part manufacturing.
5. Laser Drilling: Lasers are employed for precision drilling of small, deep, and/or complex holes in materials such as metals, ceramics, and semiconductors. Laser drilling is utilized in industries such as aerospace, electronics, and medical devices.
6. Laser Surface Treatment: Laser surface treatment processes, including laser cleaning, laser hardening, laser texturing, and laser annealing, are used to modify surface properties, enhance material performance, and create specific textures or patterns. Industries that benefit from laser surface treatment include automotive, aerospace, mold-making, and consumer goods.
7. Laser Micromachining: Lasers enable precise micromachining of small-scale features and structures on a variety of materials. This technology is used in industries such as microelectronics, medical devices, sensors, and optics.
8. Laser Inspection and Quality Control: Lasers are utilized for non-contact measurement, dimensional inspection, and quality control of manufactured parts. Laser-based measurement systems, such as laser scanners and profilometers, provide accurate dimensional data and assist in quality assurance processes.
These are just a few examples of the wide range of applications for lasers in manufacturing. The versatility, precision, and efficiency of laser technology make it a valuable tool in various processes, enabling advanced manufacturing capabilities and improved product outcomes.
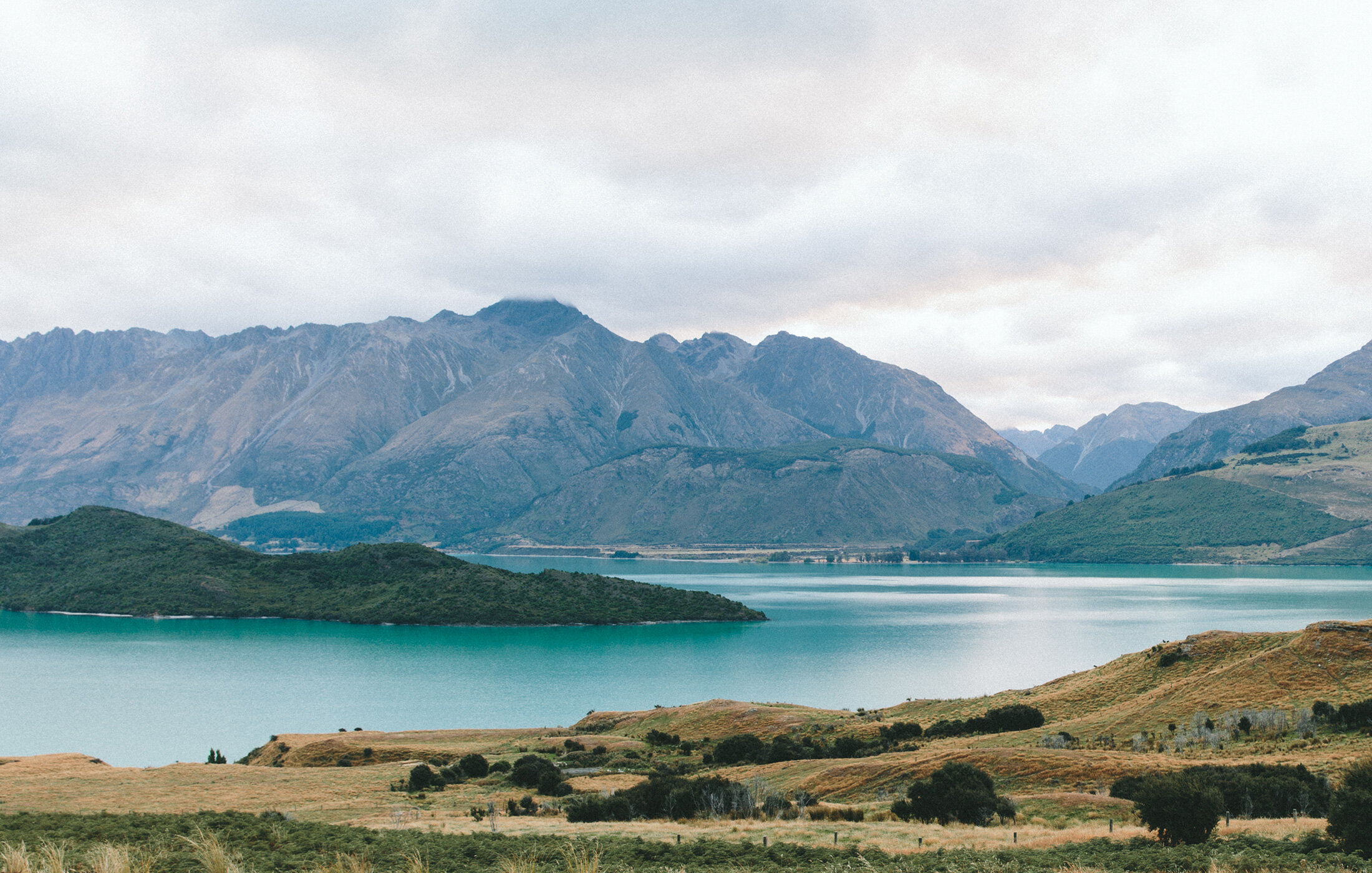
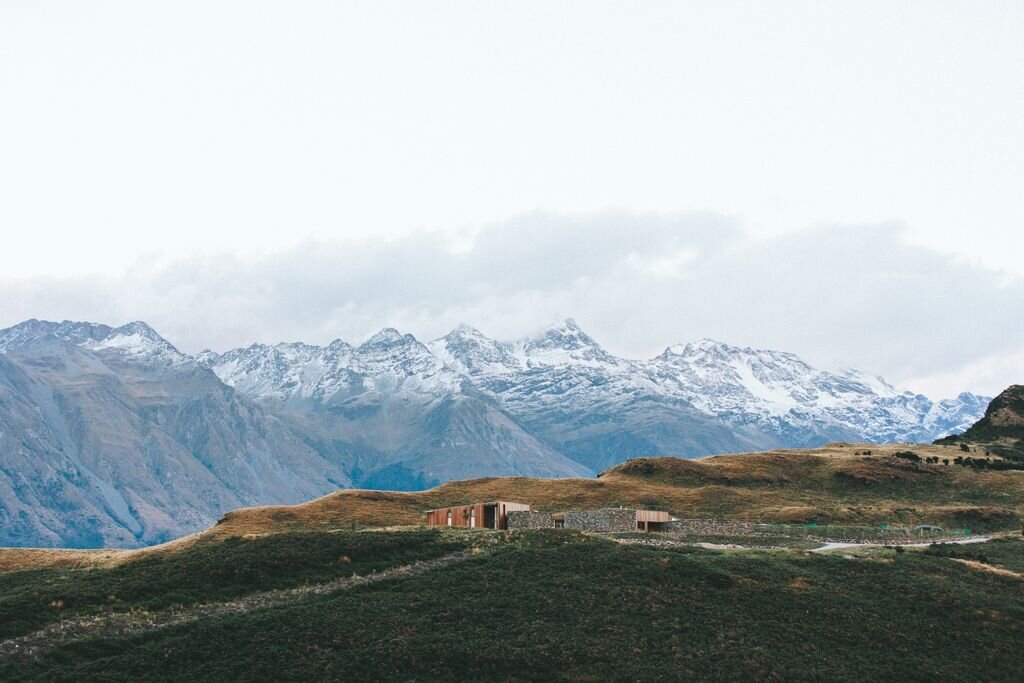
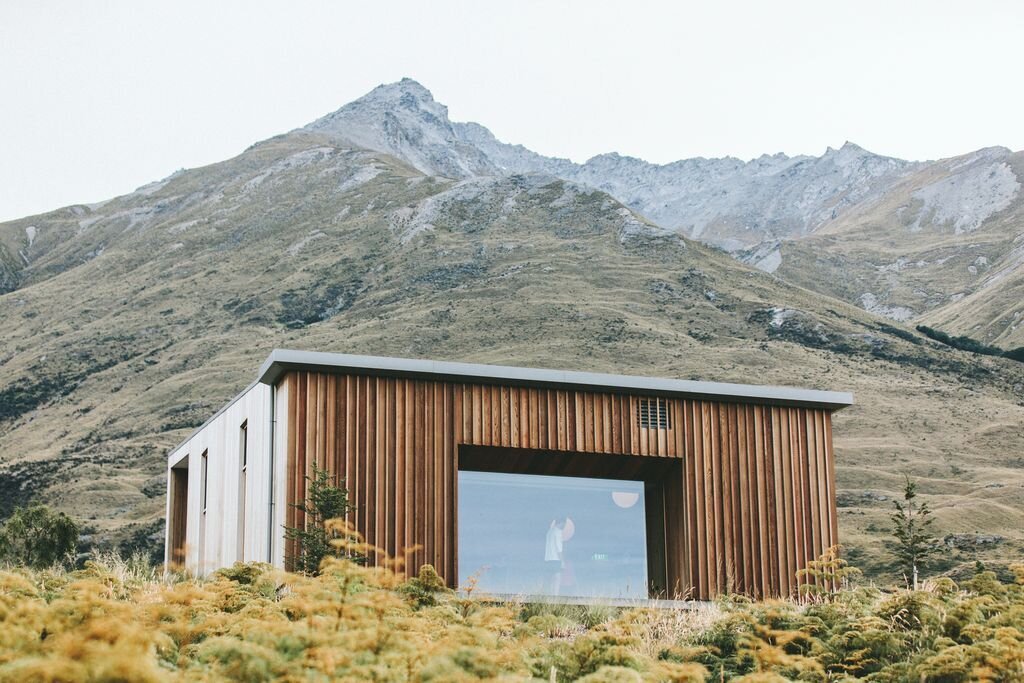
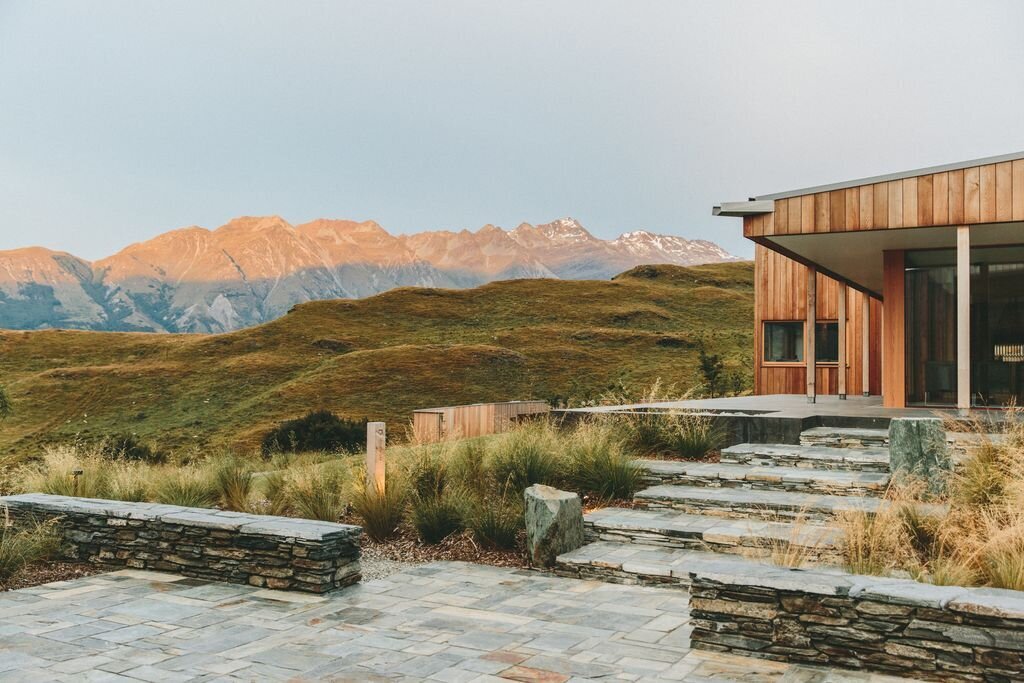
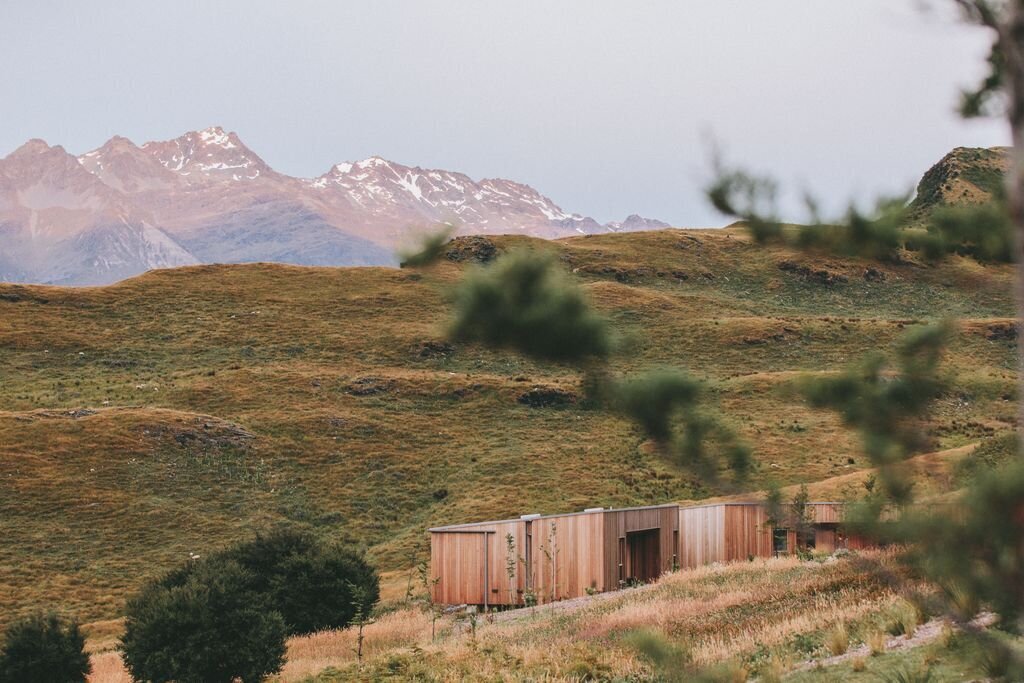
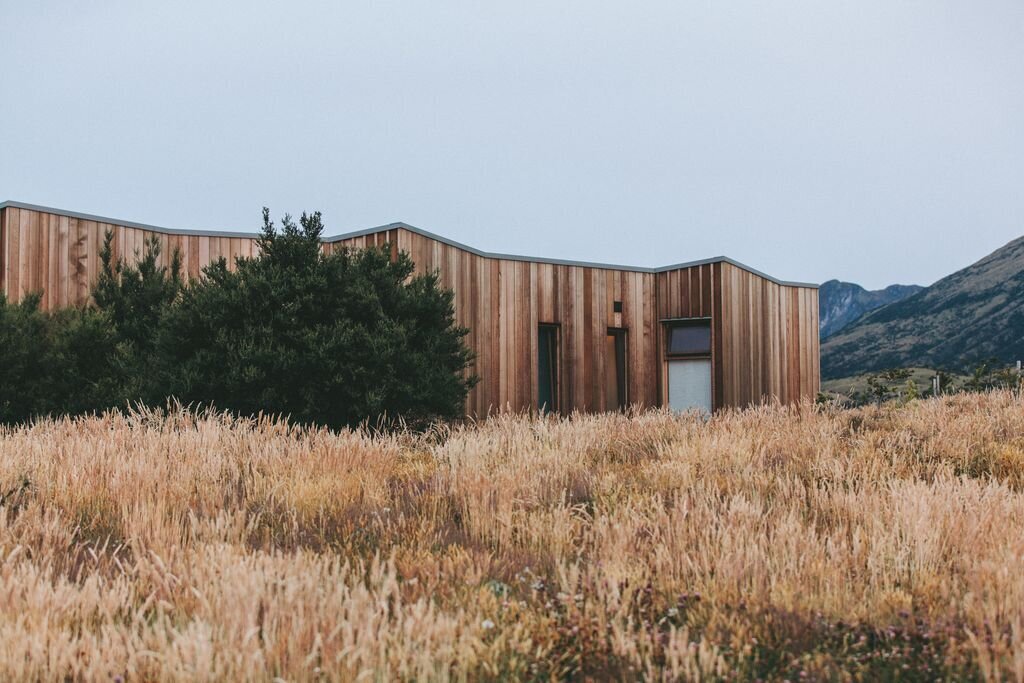