CNC MACHINING
What is CNC MACHINING?
CNC machining, also known as Computer Numerical Control machining, is a manufacturing process that utilizes computer-controlled machines to remove material from a workpiece and create custom-designed parts. It involves the use of a computer program to control the movement and operation of cutting tools, allowing for precise and automated machining operations.
Here's a general overview of the CNC machining process:
1. Design: The process begins with the creation of a digital 3D model or CAD (Computer-Aided Design) drawing of the desired part. The design specifies the dimensions, features, and tolerances of the part.
2. Programming: The CAD model is then converted into a CNC program using CAM (Computer-Aided Manufacturing) software. The CNC program contains instructions for the machine on how to move the cutting tools, the speed of operation, and other parameters.
3. Machine Setup: The CNC machine is set up by installing the appropriate cutting tools, clamping the workpiece securely, and inputting the CNC program into the machine's control system.
4. Machining Operations: Once the setup is complete, the CNC machine follows the instructions in the program to perform various machining operations. These operations may include milling, turning, drilling, boring, or tapping, depending on the design requirements.
5. Tool Path Execution: The CNC machine moves the cutting tools along predefined paths, guided by the CNC program. The tools remove material from the workpiece, shaping it according to the desired design.
6. Monitoring and Quality Control: During the machining process, the CNC machine continuously monitors factors such as tool wear, cutting forces, and dimensional accuracy. This information can be used for quality control purposes, ensuring that the final part meets the specified tolerances.
7. Finishing Operations: After the primary machining operations are complete, secondary processes such as deburring, polishing, or surface treatment may be performed to achieve the desired surface finish and appearance.
CNC machining offers several advantages over conventional manual machining:
1. Precision: CNC machining allows for highly accurate and repeatable machining operations, ensuring tight tolerances and consistent part dimensions.
2. Automation: Once the CNC program is set up, the machining process can be automated, reducing the need for manual intervention and increasing productivity.
3. Flexibility: CNC machines can work with a wide range of materials, including metals, plastics, composites, and wood. They can accommodate complex geometries and perform multiple machining operations in a single setup.
4. Efficiency: CNC machines can operate at high speeds and perform rapid tool changes, resulting in faster production times and improved efficiency.
5. Design Complexity: CNC machining enables the production of complex parts with intricate features, internal cavities, and 3D contours that may be difficult or impossible to achieve with manual machining.
CNC machining is utilized in various industries, including automotive, aerospace, electronics, medical, and many others, where precision, efficiency, and customization are paramount.
Benefits
CNC machining offers several benefits that make it a preferred manufacturing method in various industries. Here are some key benefits of CNC machining:
1. Precision: CNC machining allows for high precision and accuracy in producing complex parts. The computer-controlled machines can achieve tight tolerances and consistent quality, ensuring that the finished parts meet the desired specifications.
2. Versatility: CNC machining is versatile and can work with a wide range of materials, including metals, plastics, composites, and wood. It can handle various part sizes and shapes, accommodating both simple and highly complex geometries.
3. Efficiency and Speed: CNC machines can operate at high speeds, resulting in faster production times and increased productivity. Once the program is set up, the machining process can run continuously and autonomously, reducing downtime and increasing efficiency.
4. Automation: CNC machining enables automation, reducing the need for manual intervention and increasing productivity. Once the program is created and the machine is set up, it can execute the machining operations consistently and precisely.
5. Complex Part Production: CNC machining is capable of producing parts with intricate features, internal cavities, 3D contours, and complex geometries. This allows for the creation of highly customized and precise components that may be challenging or impossible to achieve with manual machining.
6. Repeatable and Consistent Quality: CNC machining ensures repeatable and consistent quality across production runs. The programmed instructions guide the machine precisely, reducing human error and variations in part production.
7. Flexibility in Design Changes: CNC machining offers flexibility in making design changes. Since the machining process is controlled by software, modifications to the CAD model can be easily implemented by updating the CNC program, allowing for quick iterations and design improvements.
8. Cost-Effectiveness: CNC machining can be cost-effective for both small-scale and large-scale production runs. Once the initial setup and programming are done, subsequent parts can be produced efficiently and cost-effectively. CNC machining also reduces the need for specialized tooling or molds, minimizing tooling costs.
9. Complex Machining Operations: CNC machines can perform a wide range of machining operations, including milling, turning, drilling, boring, tapping, and threading, all within a single setup. This eliminates the need for multiple machines or manual tool changes, streamlining the production process.
10. Quality Control: CNC machines often incorporate built-in monitoring systems that can measure and verify dimensions, tool wear, and machining parameters during the process. This allows for real-time quality control and ensures that the parts meet the specified requirements.
These benefits make CNC machining a preferred choice for manufacturing precision components in industries such as aerospace, automotive, medical, electronics, and many others. The combination of accuracy, versatility, efficiency, and automation provided by CNC machining enables high-quality production and design flexibility.
Design specifications
Design specifications for CNC machining are crucial for ensuring the successful and efficient production of parts. Here are some key design considerations and specifications for CNC machining:
1. Material Selection: Specify the appropriate material for the part based on its properties and intended application. Consider factors such as strength, durability, heat resistance, conductivity, and machinability. Common materials used in CNC machining include metals (aluminum, steel, titanium), plastics (ABS, acrylic, nylon), and composites.
2. Dimensional Accuracy and Tolerances: Define the required dimensional accuracy and tolerances for the part. Specify the allowable deviations in dimensions, such as length, width, height, and feature sizes. This ensures that the finished part meets the desired specifications and fits within assembly requirements.
3. Part Complexity and Features: Consider the complexity and features required for the part. CNC machining can accommodate intricate geometries, internal cavities, threads, undercuts, chamfers, and other detailed features. Clearly define these features in the design specifications to ensure their proper production.
4. Surface Finish: Specify the desired surface finish for the part. This includes considerations such as roughness, smoothness, texture, and cosmetic appearance. Different machining techniques, tooling, and post-processing methods may be required to achieve the desired surface finish.
5. Draft Angles and Fillets: Incorporate draft angles and fillets in the design to facilitate the machining process and improve part release from molds or fixtures. These features help prevent tool collisions and allow for smoother tool movements during machining.
6. Part Orientation and Accessibility: Consider the orientation of the part during machining and the accessibility of the cutting tools to all required features. Ensure that the design allows for proper tool access and clearance, minimizing the need for multiple setups or complex fixturing.
7. Tool Selection: Provide guidelines for tool selection, including the type of cutting tools, their sizes, and coatings. Different tools are suited for specific materials and machining operations. Specify any special tooling requirements, such as custom or specialized tools.
8. Tool Paths and Machining Strategy: Define the preferred tool paths and machining strategy for the part. This includes considerations such as roughing, semi-finishing, and finishing operations. Specify the cutting speeds, feed rates, and depths of cut for each operation.
9. Part Consistency and Batch Requirements: Specify the required consistency and uniformity of the parts within a batch or production run. Consider factors such as batch size, tolerances, and quality control measures to ensure consistent production and part interchangeability.
10. Design for Manufacturability: Design the part with considerations for the CNC machining process. Minimize complex setups, avoid excessive undercuts or overhangs, and ensure proper tool access. Collaboration with CNC machining experts can help optimize the design for manufacturability and cost-efficiency.
By considering these design specifications for CNC machining, you can enhance the manufacturability, quality, and efficiency of the parts, leading to successful outcomes in CNC machining processes.
APPLICATIONS
CNC machining is widely used in various industries for the production of precise and customized parts. Here are some common applications of CNC machining:
1. Aerospace Industry: CNC machining is extensively used in the aerospace industry for the production of aircraft components, including engine parts, turbine blades, structural components, and landing gear. The high precision and ability to work with complex geometries make CNC machining crucial for aerospace manufacturing.
2. Automotive Industry: CNC machining plays a vital role in the automotive industry for manufacturing components such as engine parts, transmission components, suspension components, and interior and exterior trim. CNC machining enables the production of high-precision parts that meet the stringent requirements of the automotive sector.
3. Medical Industry: CNC machining is widely utilized in the medical industry for the production of orthopedic implants, prosthetics, surgical instruments, and medical device components. CNC machining ensures the accuracy and quality required for medical applications, allowing for the customization of parts to suit patient needs.
4. Electronics Industry: CNC machining is employed in the electronics industry for producing components such as printed circuit boards (PCBs), connectors, enclosures, and heat sinks. The precise and intricate machining capabilities of CNC machines enable the manufacturing of small, complex electronic parts.
5. Tool and Die Making: CNC machining is extensively used in tool and die making, where precision and accuracy are crucial. CNC machines can produce molds, dies, jigs, and fixtures with high precision, allowing for efficient and consistent manufacturing processes.
6. Energy Sector: CNC machining is utilized in the energy sector for the production of components used in power generation, oil and gas exploration, and renewable energy systems. This includes parts such as turbine components, valves, pumps, and heat exchangers.
7. Consumer Goods: CNC machining finds application in the production of consumer goods such as jewelry, watches, eyewear, and home appliances. It allows for the creation of intricate designs, precise finishes, and custom-made products.
8. Prototyping and Rapid Manufacturing: CNC machining is widely used for rapid prototyping and small-batch production. It enables quick turnaround times, design iterations, and the production of functional prototypes before moving to large-scale production.
9. Defense and Military: CNC machining is employed in the defense and military sectors for the production of components used in weapons systems, vehicles, and defense equipment. CNC machining ensures the accuracy, reliability, and consistency required for these critical applications.
These are just a few examples of the wide range of applications for CNC machining. The versatility, precision, and efficiency of CNC machines make them valuable tools in various industries, enabling the production of high-quality, customized, and complex parts.
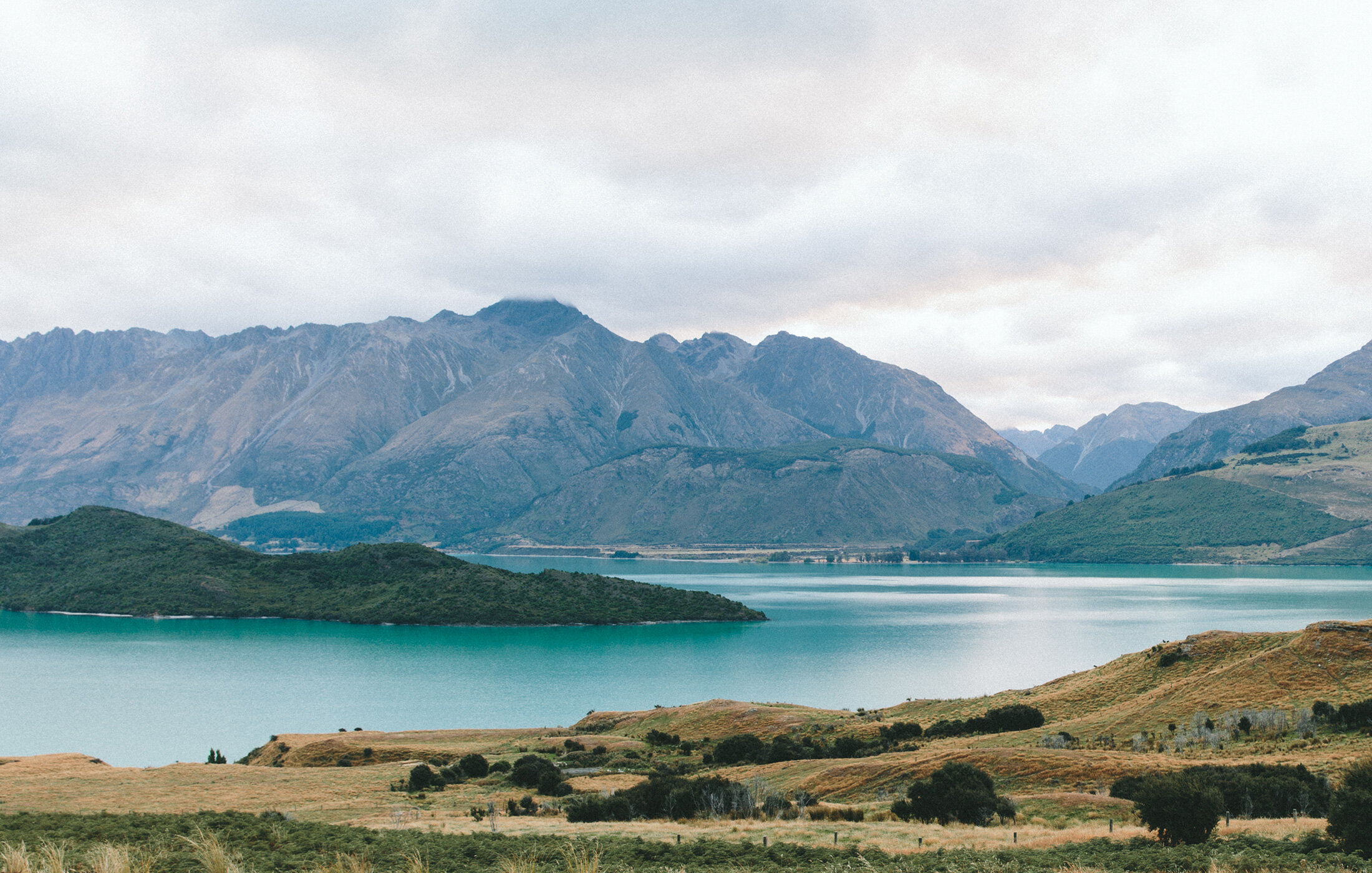
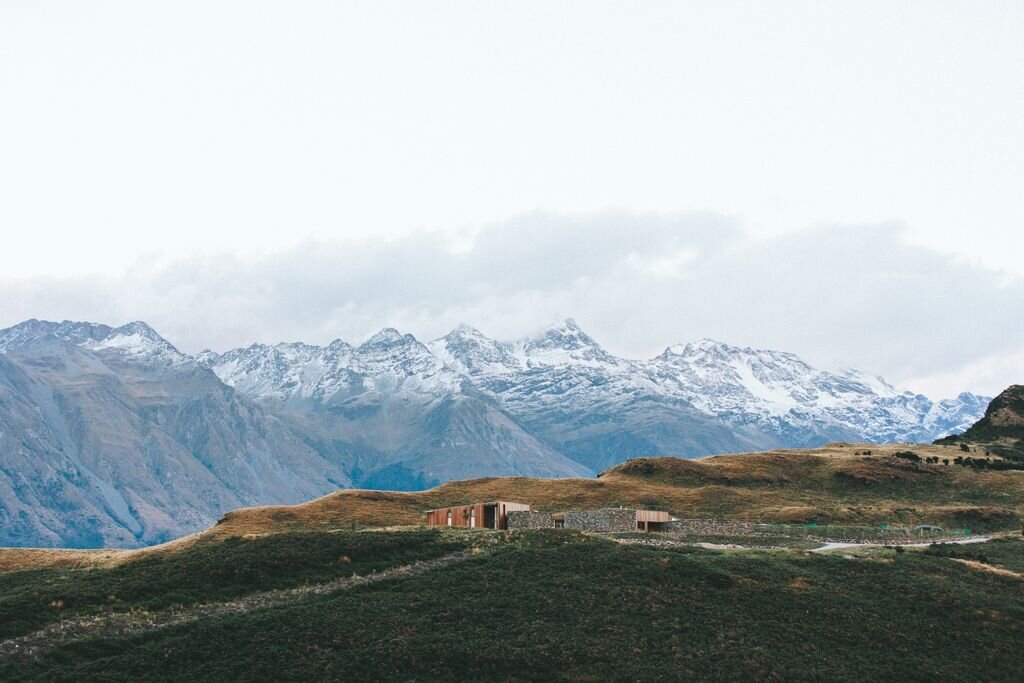
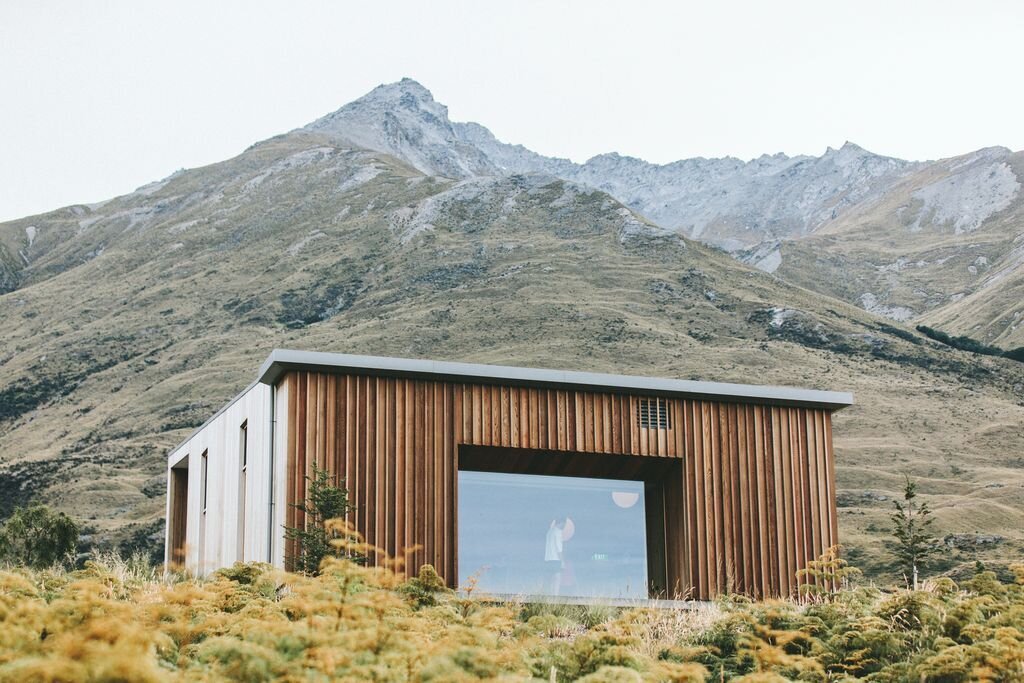
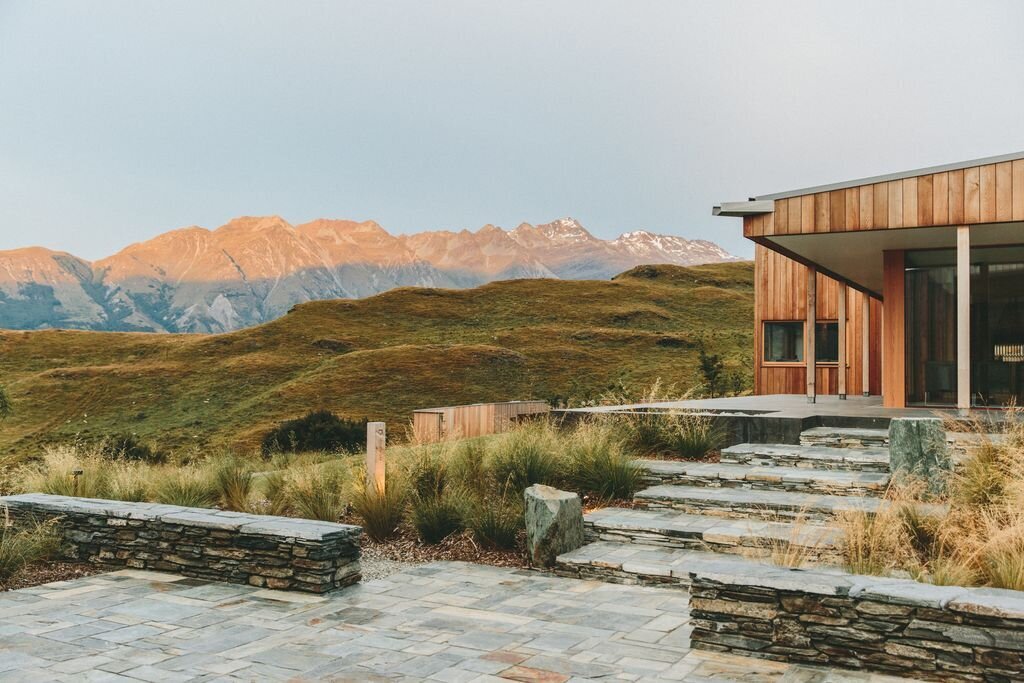
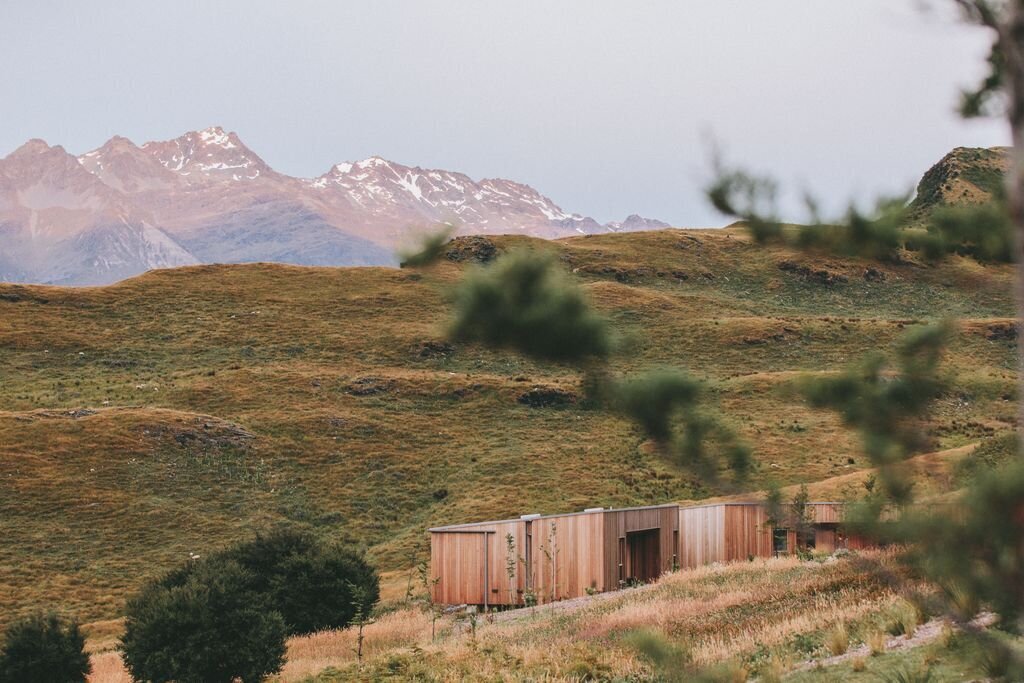
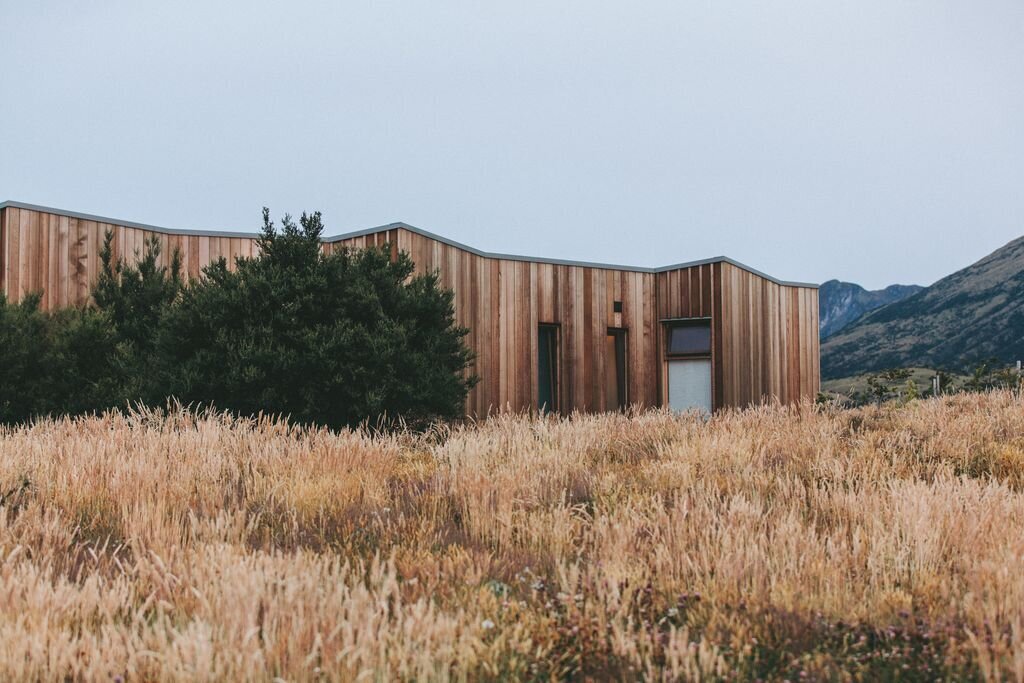